Lahti Glass Solution Clinic has proved its value to the customers by solving their different kind of challenges in batch house. One very vital topic is how to eliminate dust, when handling raw materials.
Dust can be an annoying problem in a glass production facility. It creates unpleasant working environment, malfunction of equipment and moreover; it can be hazardous for human health.
Dust is generally consisting solid particles ranging from 1 micrometer (1µm) up to 100µm, which may or may not become airborne depending on their origin, physical characteristic and ambient conditions. For occupational health measurement purposes three particle sizes are agreed internationally (CEN EN481 in EU). Those are based on penetration and deposition of different parts of human respiratory track: Inhalable fraction of dust can be aspired into nose and mouth (PM100); Thoracic fraction can penetrate to the head airways and enter to the thoracic airways of the lungs (PM10); Respirable fraction of inhaled airborne particles can penetrate beyond the terminal bronchioles into gas-exchange region of the lungs, which comprise the bronchioles, the alveolar and the alveolar sacs (PM2,5).
Hazardous respirable dust
Some of the raw materials are classified hazardous or even poisonous. Especially respirable dust of sand and quartz as well as cullet should be eliminated completely or at least minimized. Human contact of common coloring ingredients like cobalt and selenium should be avoided, too. Legislation in many countries is getting tighter to protect human health. New installations must fulfill the local requirements of respirable dust. The acceptable emission levels after the dust filters are getting tighter than previously accepted 10mg/Nm3. Especially OSHA regulation in the USA and similar legislation in the EU require much lower rates.
Holistic approach
To eliminate dust one may think that by adding dust filters to the process the problem is solved. Unfortunately that is not an adequate remedy. Much more should be considered before anything is finally installed. The whole raw material process should be designed keeping in mind, how to achieve dust free environment. The best would be a completely enclosed process – but in most cases that is impossible to achieve. Following a few examples of how to obtain cleaner environment.
Receiving hoppers
Dust emission is typically existing in such places where material is first flowing and the stopped suddenly. As an example a tipping truck is discharging dry dolomite to a receiving hopper. When the collision of dolomite happens, fine particles are carried out by escaping air. If the hopper is open, no filter can save from dust. In such case baffle type dust flaps installed to the opening of the hopper help to minimize the size of the opening by letting material to enter in but preventing air and dust to escape out only through the filter.
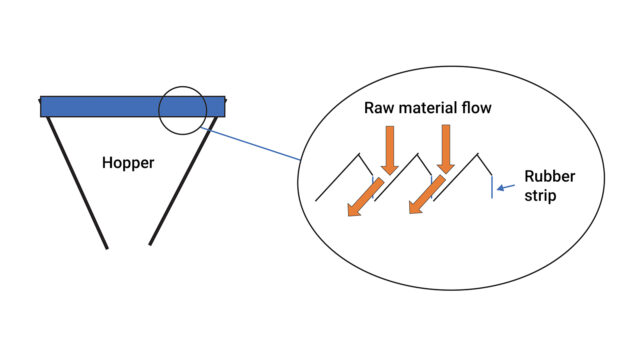
Transfer points
Another example of raw material collision is a transfer point from bucket elevator to a belt conveyor. Again the same type of sudden stop of movement release kinetic energy in the form of dust creation. The design of such point is vital: the belt conveyor must have dust cover and preferably double layer side sleaves contacting the belt as well as rubber curtains at both ends of the cover plus a filter.
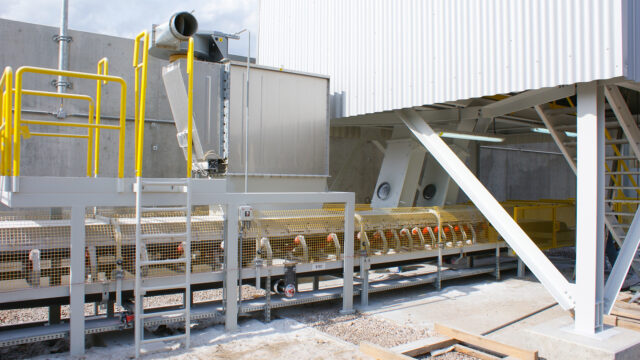
Pneumatic transfer
Nowadays most of the dry raw material are transported in tank trucks and blown pneumatically to the storage silos. When the system is correctly sized it is ideal against dust emission since it is completely closed. A common design rule is to keep the passing air speed under 1m/s. That will lead to large filtering area but the good point is, that there is no need for a blower. Special attention should be given to soda ash. It requires hydrophobic filter, like PTFE coated needlefelt. A common problem is that the truck drivers blow too much air to clean the transfer pipe in the end of the transfer. Then the necessary safety valve, protecting the silo from overpressure, opens and lets dust to open air at the silo top. There are technical means to eliminate this but once opened the safety valve must be cleaned. If not done, it continues to leak and create a big mess.
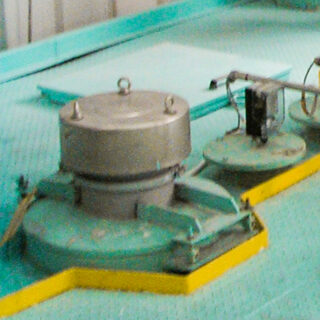
Hopper scales
Again there is point when material flow hits to a stationary wall: dosing of material to a hopper scale. When raw material is fed with a dosing feeder into the scale it replaces the same volume of air. Typically a filter sock is enough to filter the relatively small air flow. A properly sized sock is breathing well and cleaning itself: filtered dust is dropped back to the hopper at the discharge cycle of the scale. Another means is to connect the hopper scale with a duct to the following gathering belt conveyor. One must be careful with that solution, because even a small under or overpressure will cause error to the measured value of the scale.
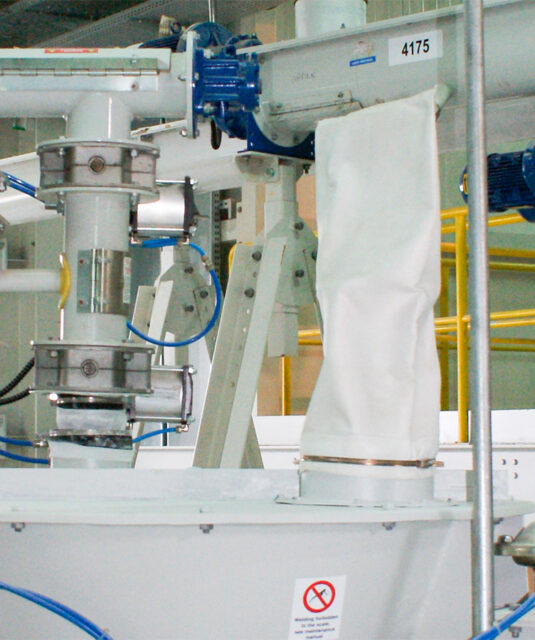
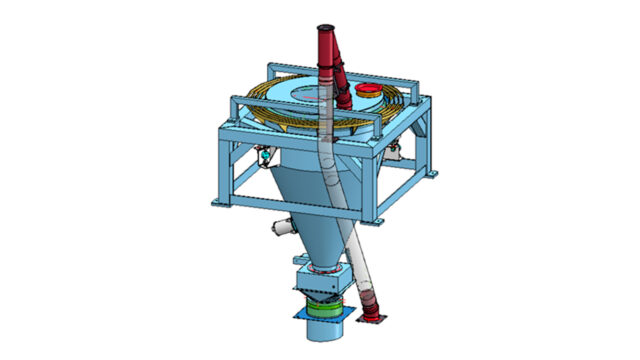
Belt conveyors
In most cases the belt conveyors are open constructions, except those transfer points earlier described herein. If the plant is so called in-line-type there is a gathering belt conveyor after dosing equipment. This belt is typically completely covered, not only the loading points. In order to prevent any leakage of material tighter spacing of rollers is necessary or a slide bottom is installed. Slide bottom replaces the rollers at loading points. That ensures dust tight connection of the belt with double rubber seals at sides of the dust cover. Some attention must put on the sizing of the drive unit of the belt conveyor since the tight rubber-rubber connection need some more power. It should be noted that the side rubbers must be adjustable to eliminate natural wear of them.
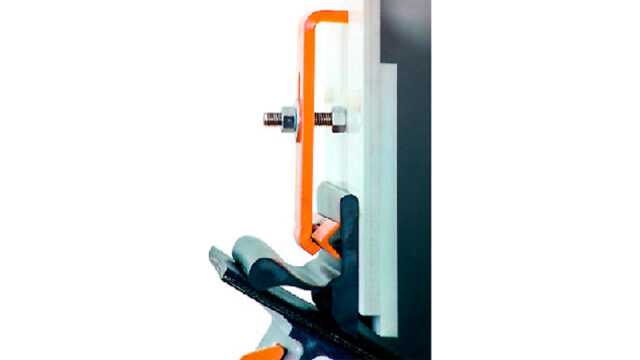
Dripping of material from the rollers is caused by poorly operating belt cleaners leaving some material on the belt. This annoying spillage is very difficult to eliminate. Proper belt scrapers are hard to find and expensive. Primary scrapers are typically Polyurethane rubber and secondary scrapers multiblade with hard metal tip. That combination works as long as those are properly adjusted but as soon as wearing occurs, they don’t in spite of spring tensioning or related means. Lifetime of the belt may be compromised if the secondary scraper is too tightly adjusted. Lahti Glass has some good experience in using a special type scraper which can be retrofitted to the existing belt conveyors, too.
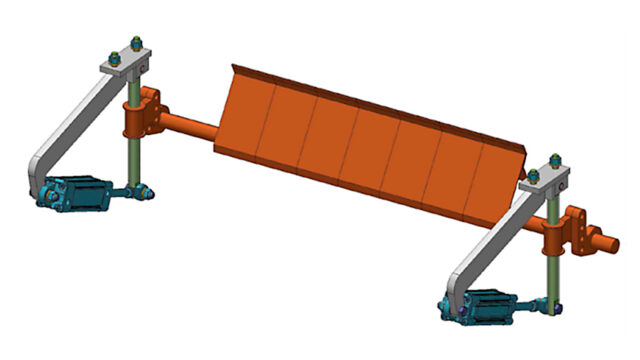
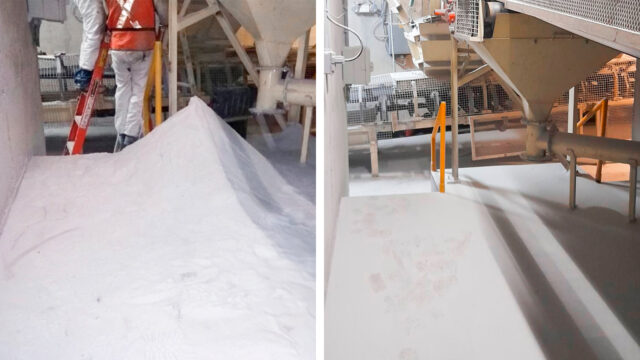
Dust filters
When the design of the process and material flow is properly done, air flow needed to ensure suction of dust is reduced to minimum. That means smaller fans for the filters and savings in investment and energy costs. The two basic solutions are individual filters for suctions points and centralized filters and ductwork to suction points. The individual filters are more common nowadays because the ductwork is prone to wear and tear and difficult to keep in balance so that each suctions point works effectively all time. But in such cases, like in cullet return lines, it may be necessary to collect fine dust away from the material stream. Then it is important to design the suction points and ducts carefully. Poor design will lead to inefficiencies like settling of dust inside the duct or high wear rate of the bends and dampers of the ducts. It is important to keep the velocity of air low so that the small cullet particles will not get airborne but high enough to float and move the fine dust particles. Typical solution is so called winnowing tower as shown in the picture below.
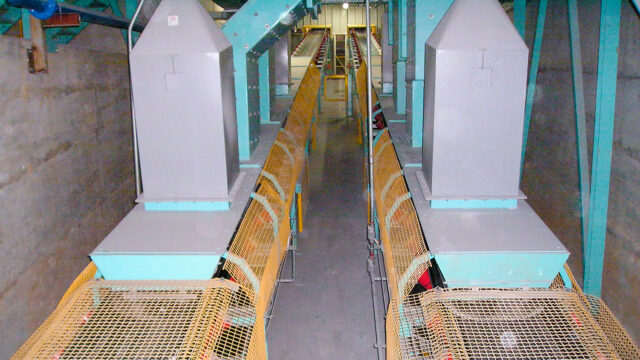
Monitoring of exhaust air to detect burst filter bag is possible with a dust detector. Also the pressure difference between dirty and clean side can be monitored to give indication of an unhealthy filter media. It should be noted that the filter canvas works best, when it is dusty since the dust particles stick better on dust itself than on fibers of the canvas. But naturally blocked canvas does not let air though. Filters are typically having compressed air cleaning (counter flow jets) or unbalances drive to vibrate and drop accumulated dust down from the canvas, which is typically 500g/m2 polyester needle felt.
As discussed herein with some examples the topic requires holistic approach. Dust elimination is an important issue, which must be part of the design of the raw material handling process in the batch plant and in the cullet return system. A properly designed system keeps the investment and running costs low. Dust free environment is possible to achieve. That requires concentration to each detail along the material flow. But it is equally important to design the process so that maintenance is easy and there is a good and safe access for adjustment and replacement.
Housekeeping is vital as well as periodic observations. Even a small hole in a flexible joint can quickly cause a raw material leakage and spreading of dust to the environment. Such annoying spillage can be prevented only by replacing those parts before they are worn out. Preventive maintenance program should be in place in the plant and supervised by the plant management.